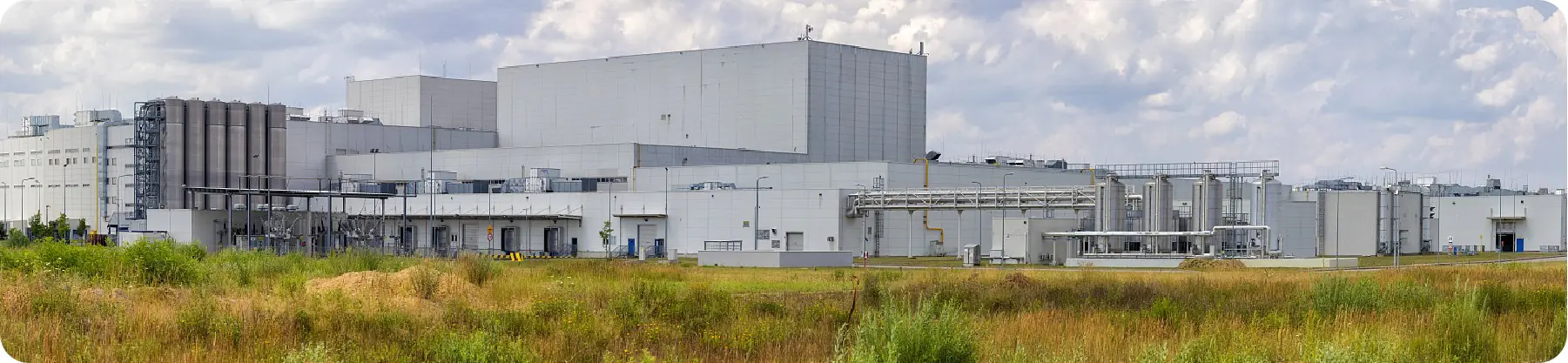
1. Overview of Rubber Magnet Products
Definition and Basic Structure
Definition of Rubber Magnets
Rubber magnets are composite materials made by combining magnetic powders (such as ferrite or rare – earth magnetic powders) with polymer rubber matrices (like NBR or EPDM) through processes like mixing and calendering. They possess both permanent magnetic properties and the elasticity and processability of rubber, and are widely used in advertising stickers and motor accessories.
Role of Magnetic Powder
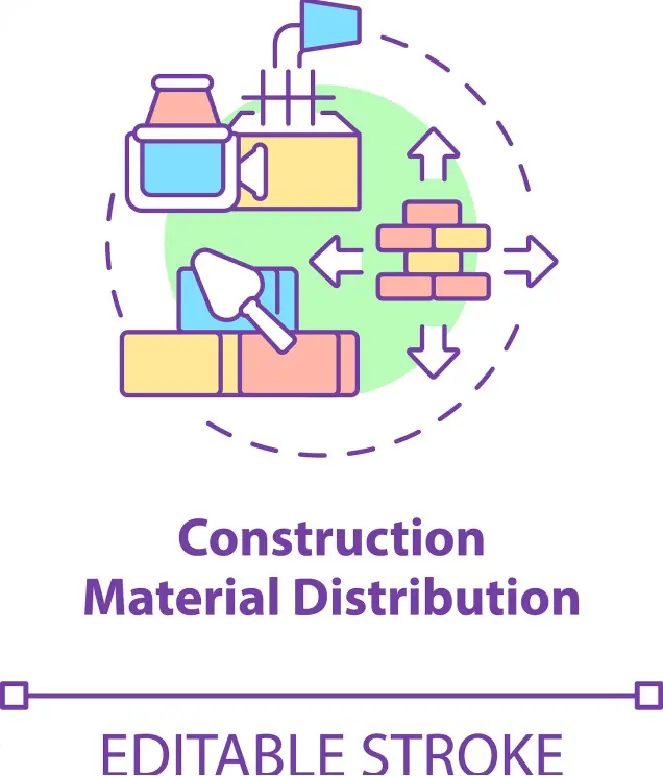
Function of Rubber Matrix
Effect of Additives
Additives, less than 5% of the total, include plasticizers (e.g., DOP for better flexibility), anti – aging agents (e.g., RD for anti – aging), and coupling agents (e.g., silane to enhance the bonding between magnetic powder and rubber). They improve processing or usage performance in a targeted way.
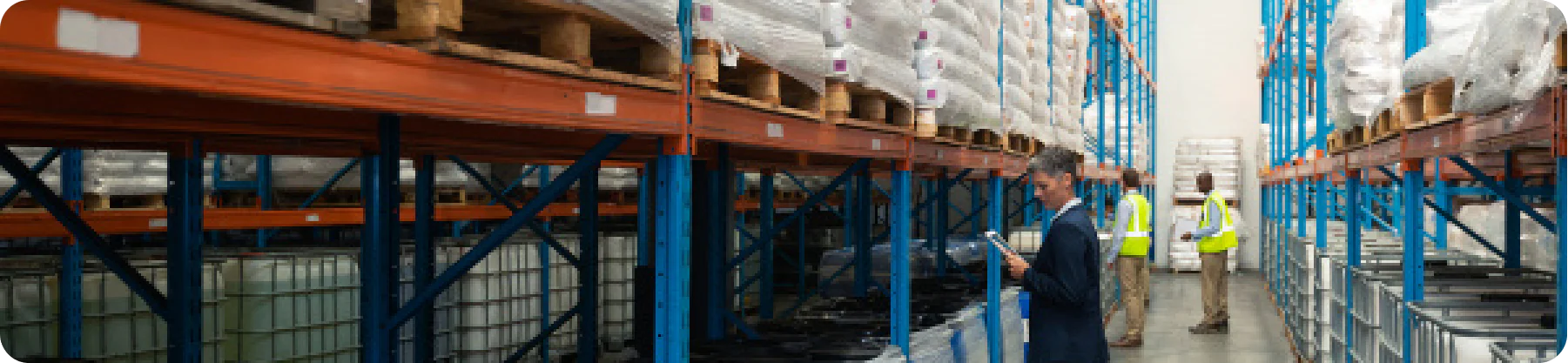
Product Classification and Common Forms
Classification by Magnetic Powder Type
Classification by Shape
aication by Magnetization Direction
Single – sided magnetization (magnetism concentrated on one side) is suitable for adsorption scenarios; double – sided magnetization (magnetism on both sides) is used for double – sided fixation; multi – pole magnetization can meet more complex application needs, such as in some high – precision sensors.
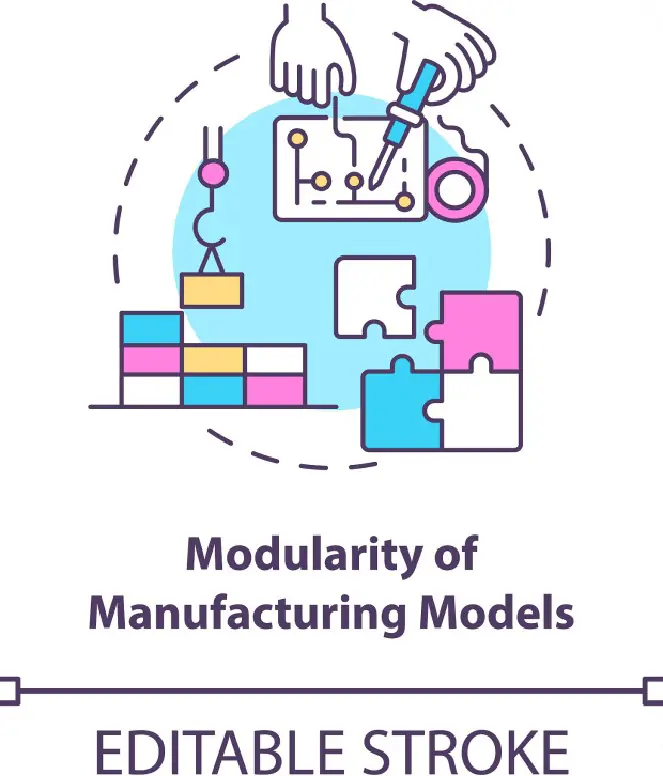
2 .Core Performance and Technical Parameters
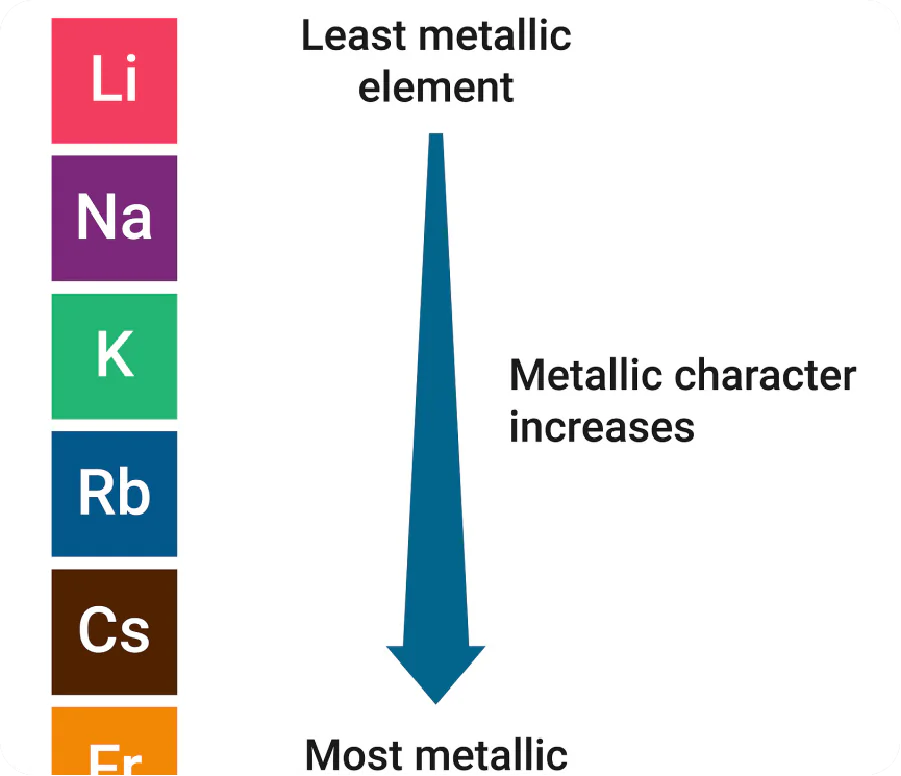
Residual Magnetism (Br)
Analysis of Key Magnetic Performance Indicators
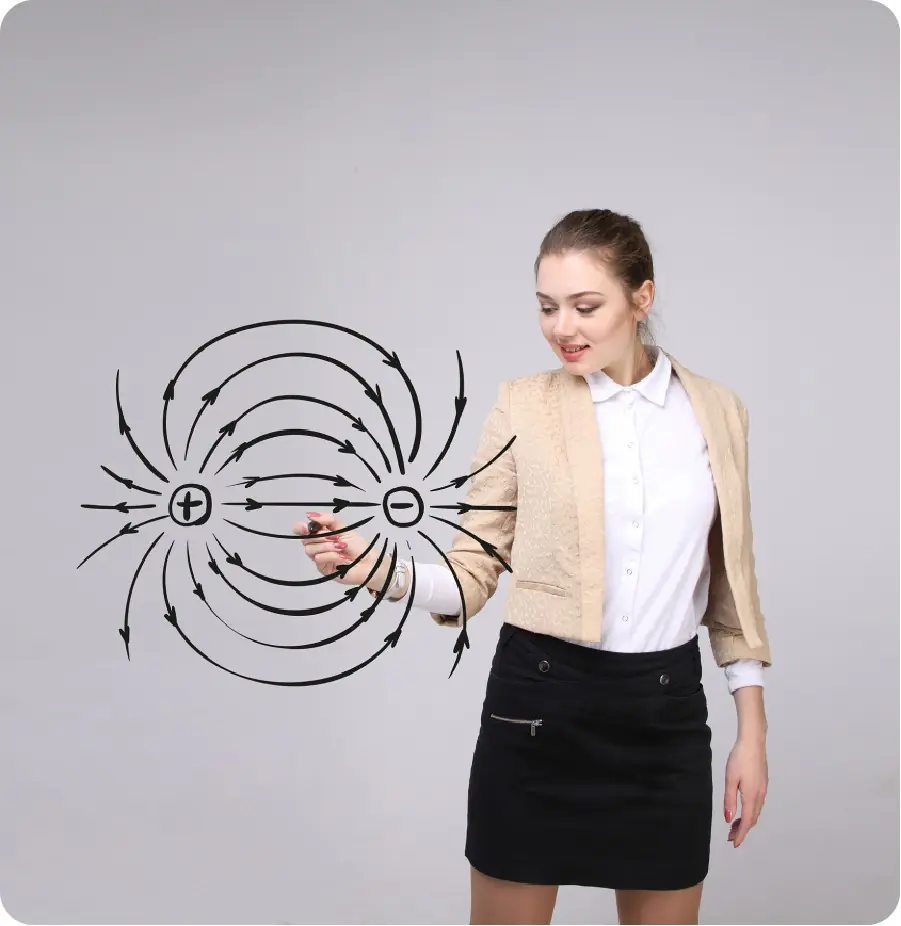
Maximum Energy Product (BHmax)
The maximum energy product (BHmax) is the maximum value of the product of the magnetic field strength and magnetic induction intensity inside the magnet. Low – performance products have a BHmax of about 10 – 20 kJ/m³, mostly used in toys. High – performance products can reach 30 – 40 kJ/m³, suitable for fields such as motors and magnetic levitation devices that require efficient energy conversion.
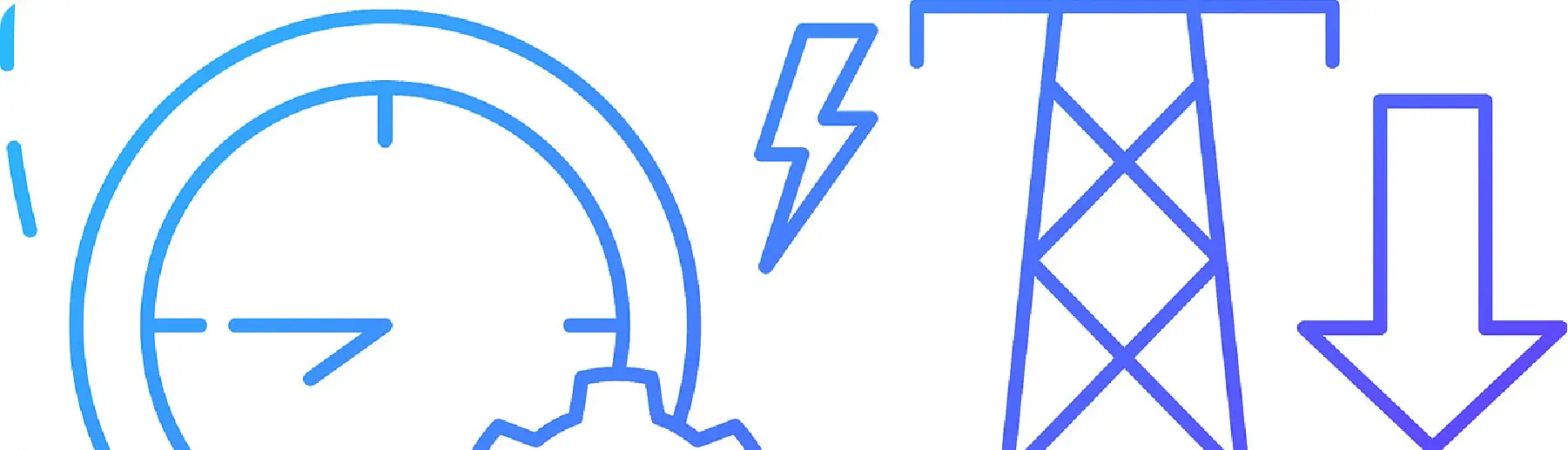
Hardness (Shore A)
The hardness of rubber magnets is usually Shore A 50 – 80. Soft – grade products with 50 – 60A can fit curved surfaces (such as curved advertising boards), while hard – grade products with 70 – 80A are suitable for industrial fixtures that require structural support, balancing flexibility and deformation resistance.
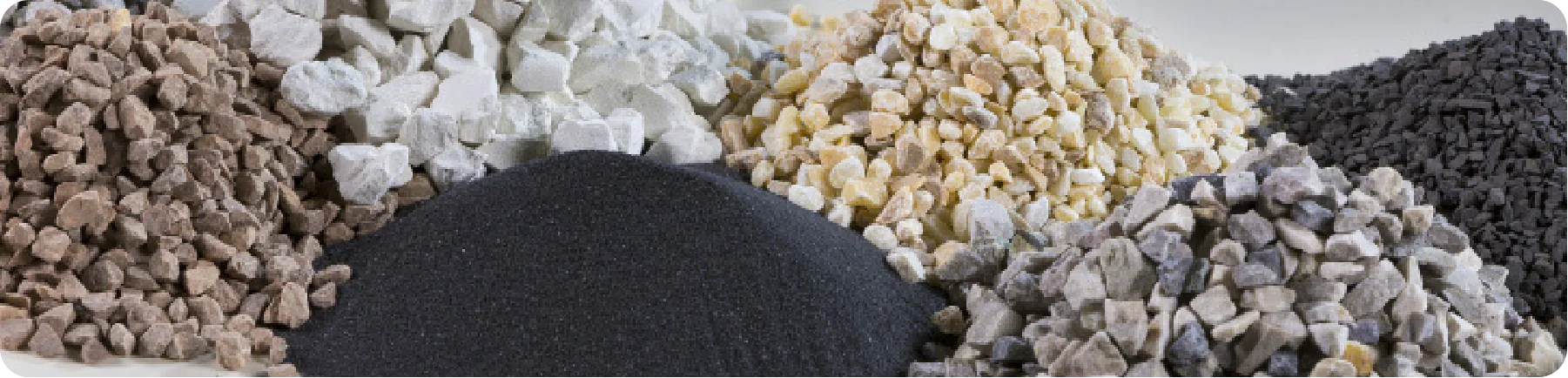